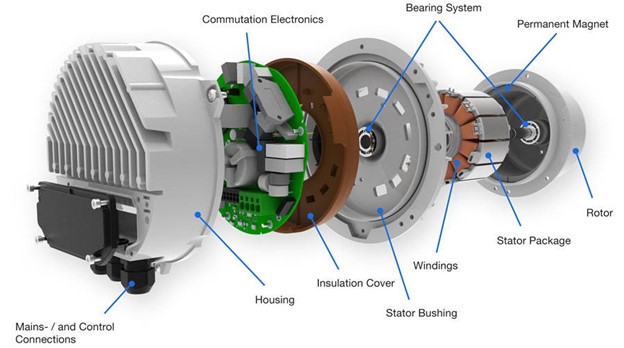
ECM (electronically commutated motor) motors are one of the advancements the HVAC industry has made in furnaces within the last few years. One of the goals of HVAC research is to find ways to increase the energy efficiency of systems to benefit homeowners, businessowners, and the environment as well. ECM motors will soon be the standard in all furnaces but unfortunately, few homeowners understand the benefits of an ECM motor or how they work. ECM motors were first introduced by GE in 1985 and are an energy-efficient alternative to PSC motors. An ECM motor is a brushless DC motor that uses electronic controls to regulate its speed, torque, or power output without external devices or sensors. An ECM motor is programmable and can maintain energy efficiency across a wide range of speeds while maintaining proper air flow through the system. Whereas PSC (permanent split capacitor) motors only turn on and off at constant speeds. In this article we will discuss how an ECM motor works and the different types of motors.
How Does an ECM Motor Work?
An ECM motor is controlled by a microprocessor, the key component that makes them able to provide higher efficiency. The microprocessor calculates the motor’s speed and torque to regulate the airflow. The rotations per minute of the motor will either ramp up or ramp down to keep the air flow steady. An ECM furnace differs in how it distributes heated air. A normal furnace uses a blower fan with two settings: on and off. Either the fan blows at full speed, or it does not blow at all. On the other hand, an ECM furnace can operate at virtually any speed between on and off. This allows for the furnace to operate at max efficiency, rather than the motor running the fan at the same constant high rate, it modulates to adjust for conditions, sometimes running at lower speeds and using less power than full load. Magnets drive an ECM motor. The motor’s rotor is a permanent magnet, and a series of electromagnets or coils line the inside of the motor’s stator. The controller applies power to sections of the coil to energize it. The opposite poles of the rotor are attracted to the coil section, and the rotor rotates. Then, the next coil section energizes to draw the rotor and turn it. This process occurs along the coil’s areas again and again in quick succession to spin the rotor.
ECM Blower Motors Types
Each manufacturer will program the ECM depending on what the motor will be used for. Motors can be programmed to maintain torque, airflow, or speed.
Constant Torque ECM
A constant torque ECM is programmed to maintain the same amount of torque regardless of the static pressure in the HVAC system. If the pressure increases, then it increases power to maintain the same torque. A constant torque ECM will maintain more airflow, than a PSC motor when there is air restriction in the system from dirty air filters from lack of maintenance or ducts. Constant torque ECMs are commonly used as blowers in air handlers. They can replace PSC motors, because they are more efficient and cost less than other types of ECMs.
Constant Airflow ECM or Variable Speed
Also known as a constant CFM motor this type of motor is programmed to maintain the same amount of airflow regardless of pressure. It will increase torque and speed to maintain the same airflow when there is an increase in pressure in the HVAC system. Constant airflow ECMs are used in high efficiency furnaces and air conditioners. They are true variable speed motors and the cooling and heating capacity are unaffected by dirty air filters, dirty air handlers, or high demand.
Constant Speed
Constant speed ECMs are also known as constant RPM. This type of motor is programmed to maintain the same speed regardless of static pressure in the HVAC system. If airflow is restricted, it will increase its torque to maintain the same speed. Constant speed ECMs are typically used for AC condenser fans.
Advantages of an ECM Motor
Energy Savings
ECMs use less wattage than a standard motor. ECMs are between 65% to 75% efficient, in contract PSC motors are only about 45% efficient. This translates into lower operating costs.
Longer Lifespan
Not only do ECMs have a longer lifespan of about 10 years of service but they require less maintenance as well. ECMs contain true ball bearings that do not require routine lubrication. They also sustain less wear and tear due to gradual acceleration and deceleration, and they are overall less likely to overheat. Remember they are also brushless so there are no brushes that wear out or spark.
Increased Comfort
Since ECMs run longer cycles they can maintain consistent temperatures without drastic temperature dips and spikes. A conventional furnace which operates at 100% fan speed will often raise your indoor temperature too quickly.
Increased Indoor Air Quality
Another benefit of ECMs longer cycles is improved indoor air quality. Longer cycles result in extended periods of air filtration to remove allergens and other pollutants from the air while also ensuring optimal humidity levels.
Disadvantages of an ECM Motor
The main disadvantage of an ECM is the cost. Also, if any part of the motor fails, it could result in longer downtime of the entire system until the motor is replaced as the issues cannot be bypassed to keep the system running.
Contact LA Construction, Heating and Air
With an ECM you save money on operating costs while also benefiting from improved indoor comfort and air quality. For more information about furnace replacement give us a call today or contact us online for a free consultation. We also offer furnace repair and maintenance plans to fit your needs.